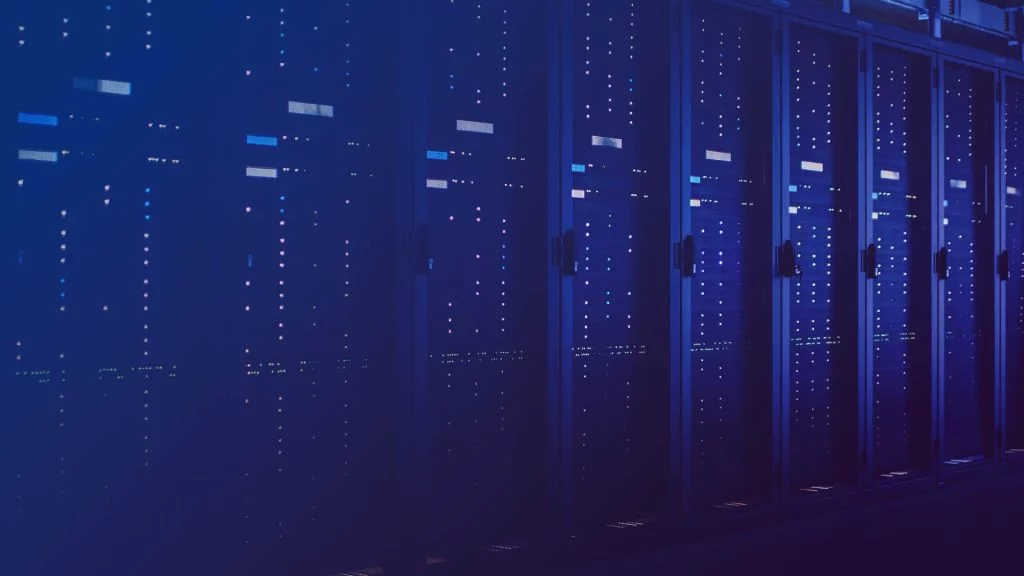
Cloud Manufacturing MES
Cloud manufacturing One secure location for all your production data What is Cloud Manufacturing? Cloud manufacturing is the application of cloud computing in manufacturing. It
MES System is a manufacturing efficiency and execution platform that allows for the collection of data from the machines, or entire production line, analysing and displaying them in a user-friendly manner. MES software is implemented to make operators’ jobs more predictable and help managers undertake more insightful decisions for faster and better production.
The difference between Manufacturing Execution Systems (MES) and Enterprise Resource Planning (ERP) systems lies in their core functionalities, focus areas, and operational scope within an organization. While both systems are pivotal in modern business management and aim to increase efficiency and streamline operations, they serve distinct roles within an enterprise.
Feature |
MES (Manufacturing Execution System) |
ERP (Enterprise Resource Planning) |
---|---|---|
Focus |
Specific to manufacturing processes and shop floor operations |
Broad, integrates various business processes across the entire organisation |
Primary Objective |
Optimising and monitoring production processes in real-time |
Streamlining and integrating all business operations |
Key Functions |
Real-time production tracking, quality control, machine efficiency |
Financial management, supply chain management, HR, CRM |
Scope |
Operational control at the production level |
Strategic management and planning at the organisational level |
Data Handling |
Detailed, operational data focused on manufacturing |
Aggregated data across various business functions |
User Base |
Primarily used by production managers and shop floor personnel |
Used by various departments including finance, HR, sales, etc. |
Impact |
Directly affects production efficiency and product quality |
Affects overall business efficiency, resource allocation, and strategic planning |
Production stoppages.
Lack of knowledge about the current progress and work of production.
Waste of paper, difficulty maintaining versioning and access to documents.
Long production start-up times.
Human errors.
Inadequate reporting on performance data.
Unable to take proactive decisions on problems and solutions.
Ineffective process control and failure to meet customer expectations.
Production not shipped on time.
Inability to identify bottlenecks in the production process.
Manual production planning, planning in Excel.
Not sure that I have all the resources to produce.
Poor tracking of production and production order fulfilment.
Uncontrolled production of defects.
Inadequate traceability of production processes.
Too many scrap and defects.
Manually generated SPC reports.
Lack of immediate information about the failure in the maintenance department.
Too much downtime.
No windows available for inspections and repairs.
Lack of system integration
Multiple systems across one. facility instead of one.
Lost access to the prodution system.
There is no data to make a good decision.
Lack of control over the implementation of production.
The need to work on additional shifts due to the failure to cope with the current production.
The software can lead to the identification of more than 200 processes from the shop floor to the warehouse to get rid of or to simplify, e.g. quality documentation forms with redundant information. Step by step, combining small changes can add up to considerable improvement potential. Properly adresssed issues can lead to time savings reduction ranging from 10 minutes up to 2 hours. Not only it helps to reduce the burden for employees in production but also for those surrounding work areas involved in cross-divisional processes.
OEE & OTIF increase
✔️ predicted date time of last item in production/sales order
✔️ less and faster changeovers
✔️ faster execution of production tasks
Less defects
✔️ faster defects recognition and rework management
✔️ SPC and condition-based monitoring
✔️ periodical quality plans
Traceability
✔️ BOM validation (item check, if QC release)
✔️ tools life cycle monitoring
✔️ up-stream and down-stream
Manufacturing in the region for the region, next to our customers is a pillar of our operations strategy.
We invested massively in our factories over the last years to increase capacity; completing these investments with the best digitalization solution of all manufacturing systems is a key part of our program toward more efficiency and agility. In a great collaboration with ANT, we are rolling out our plans.
Fabrice Revert, COO
LinkedIn
OEE, production and quality monitoring is very precise and automatic. The process optimisation is less time consuming and problems are faster and easier to detect.
ANT managed to custom the MES interface and its funcionalities to a high degree so that we could really make the most out of the system
Veronica Ottonello, Industrial Process Engineer at Bormioli Pharma
LinkedIn
Cloud manufacturing One secure location for all your production data What is Cloud Manufacturing? Cloud manufacturing is the application of cloud computing in manufacturing. It
Manufacturing Execution System (MES) and Enterprise Resource Planning (ERP) complement each other perfectly in production companies. However, these systems have different usage. ERP is mainly
Lean manufacturing is a production process that is based on the concept of maximizing productivity while minimizing waste within manufacturing. During the course of this
Why ANT?
ANT is an independent software provider for modern manufacturing. Our solutions are designed to make production facilities more flexible, adaptable, and efficient. The software enables real-time visibility into your operations and facilitates collaboration between people, data, and systems so that you can spend less time on operational tasks and more time on innovation.
Contact with our Expert
Why to get a demo?
We can suggest several indicators suggest it’s the right time to consider implementing an MES:
Further reading: Why OEE drops after MES implementation?
The implementation of a MES system is a complex and costly process that requires careful planning and preparation. A key step is to conduct a
The American corporation Gartner conducts a series of market studies, the results of which are presented in the final version in a report called Gartner
MES is now undoubtedly the basis of digitalization and the foundation of modern manufacturing activity. In the environment that can be described as Industry 4.0,
The price of a professional MES system depends on the selected list of functionalities, integration with machines and required equipment (i.e. printers, scanners and computers). The total cost will depend on the company’s needs and the number of machines that need to be connected to achieve business results. The MES system is unlimited, modular and scalable, and is not tied to a specific number of users or devices, and can therefore be customized to meet the needs of any company.
By providing your email and clicking the “Sign up” button, you agree to subscribe to our newsletter to receive the latest news and useful insights about manufacturing.
By providing your email and clicking the “Download a catalogue” button, you agree to receive our newsletter.