The pharmaceutical industry is one of the most demanding manufacturing industries. The combination of high process efficiency associated with the high volume of medicines produced, while maintaining the highest quality standards in compliance with strict regulatory standards, plays an important role here.
An effective way to maintain high production efficiency is to implement improvements and respond to changes based on the monitoring of the overall production efficiency index (OEE). Data is collected in real time, allowing areas for improvement to be identified at short notice. Eliminating bottlenecks located in this way contributes to increasing machine availability, reducing micro-downtime and thus increasing OEE.
The OEE monitoring system can be implemented within 3 months, without the need for validation, a task we carried out at one of our clients operating in the pharmaceutical industry.

Monitoring Production Efficiency – OEE monitoring system capabilities
The OEE monitoring system allows data to be collected from machines and equipment. Depending on the equipment on the line, this is done through PLC sensors, signal duplication or the installation of sensors in the form of external devices. The data collected is essential for further analysis and the generation of real-time OEE reports, so correct data collection plays a key role in the performance monitoring process.
When choosing a partner to implement the software, it is worth considering their experience in machine integration. The selection of a suitable method of integration with machines and the correct installation of high-performance sensors ensures that the reports and analyses created on the basis of the collected data will reflect the actual situation on the production floor.
Why invest in efficiency improvements?
Imagine the case of an increase in OEE from 40 to 50%. This results in an increase in production volumes of 25%. If the company has 4 production lines, such an increase in OEE means the equivalent of one additional line with the same machinery and number of employees.
The implementation of the system at the client’s site allowed real-time calculation of OEE and access to historical data to track progress. The system has also facilitated a reliable root cause analysis of production performance – detailed reports make it possible to analyse losses, types of downtime and breakdowns, and thanks to the data in the Pareto chart, it was quickly found out which events generate the greatest delays. The dashboards installed on the production floor made it possible to view current production and to react quickly in the event of apparent problems with the correct execution of processes. In the case of the implementation of a production efficiency monitoring system in the pharmaceutical plant discussed in this article, there was an increase in OEE from 44% to 54%.
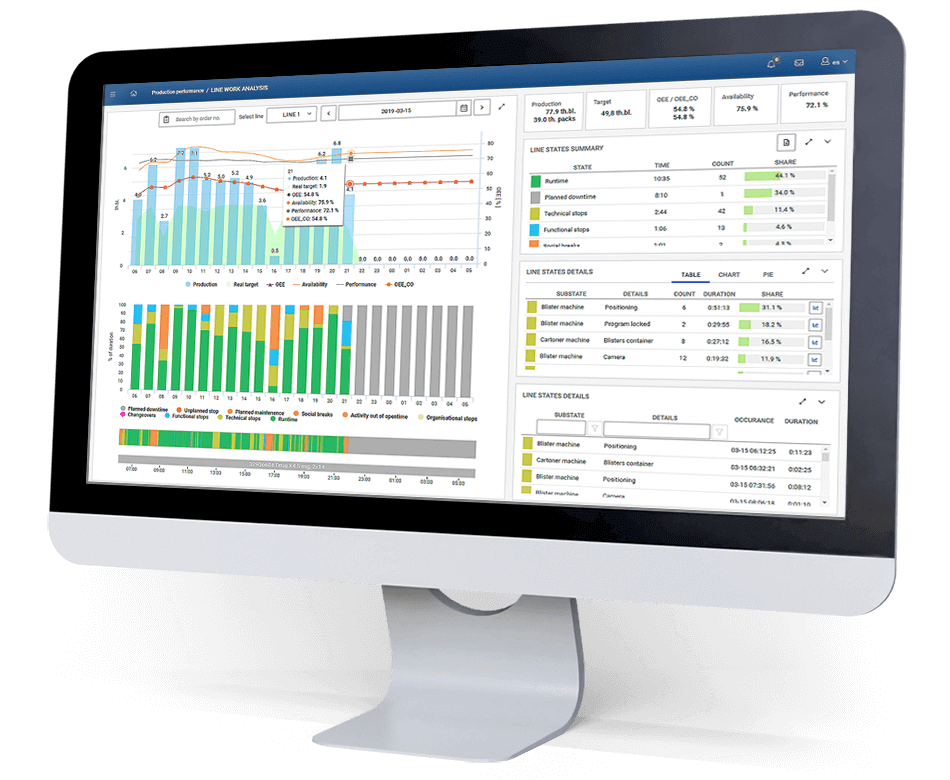
What about the validation of an OEE monitoring system? This type of software does not necessarily need to be validated, although it can be beneficial in certain situations. In the case of OEE monitoring, this is not required as the production process, product quality and patient health are not affected, and data is collected on a one-way basis. If monitoring is only needed for internal purposes, such as tracking performance and identifying areas for improvement, validation is not necessary. It is enough to be sure that the system is properly calibrated and working properly. Validation, on the other hand, is necessary if the system is used for batch report generation, quality control or the system guides operators through the BULK process. Validation is therefore performed at the time of software development for the MES system. Electronic batch reports (EBR), quality checks carried out in the system, as well as material validation and BULK handling require the reliability of the software to be demonstrated to monitor production efficiency.
Example of implementation of OEE monitoring of packaging lines without validation in 3 months in a pharmaceutical company
We performed the implementation of OEE monitoring of packaging lines in a pharmaceutical company. The scope of the system included:
-
- OEE monitoring for 7 blister packing lines,
-
- monitoring of micro-breaks,
-
- integration with SAP,
-
- installation of equipment: Data Activation, Operator Panels, TV.
The company wanted to achieve the following business objectives:
-
- automatic downloading of real-time data,
-
- increasing the availability of production lines,
-
- reduction in micro-breaks,
-
- reducing Maintenance’s response time,
-
- the possibility of introducing an Electronic Series Report.
Machine data was downloaded through direct integration with Beckhoff and Siemens S7-1200 and S7-300 controllers. Data was downloaded from machines/equipment such as the blister machine, checkweigher, serialiser and cartoner. The data collected reported, among other things, on products accepted and rejected, automatic, manual and emergency stops or alarm messages. Data collection was done in a process-neutral manner.
During the implementation in question, ANT was responsible for the entire process, including hardware installation, cable routing, system implementation and ERP integration. The implementation schedule comprised 12 weeks of work, and the completion of the work at each stage is shown in the schedule below.

We performed a comprehensive implementation. As a service provider, we handled all processes from project start-up and analysis to testing and launch. The direct exchange of information with the client at each stage of the work allowed us to streamline communication, so that we met all the expectations of the client. As a result, after 12 weeks, the client received from us tested and ready-to-run software, without the need for system validation.
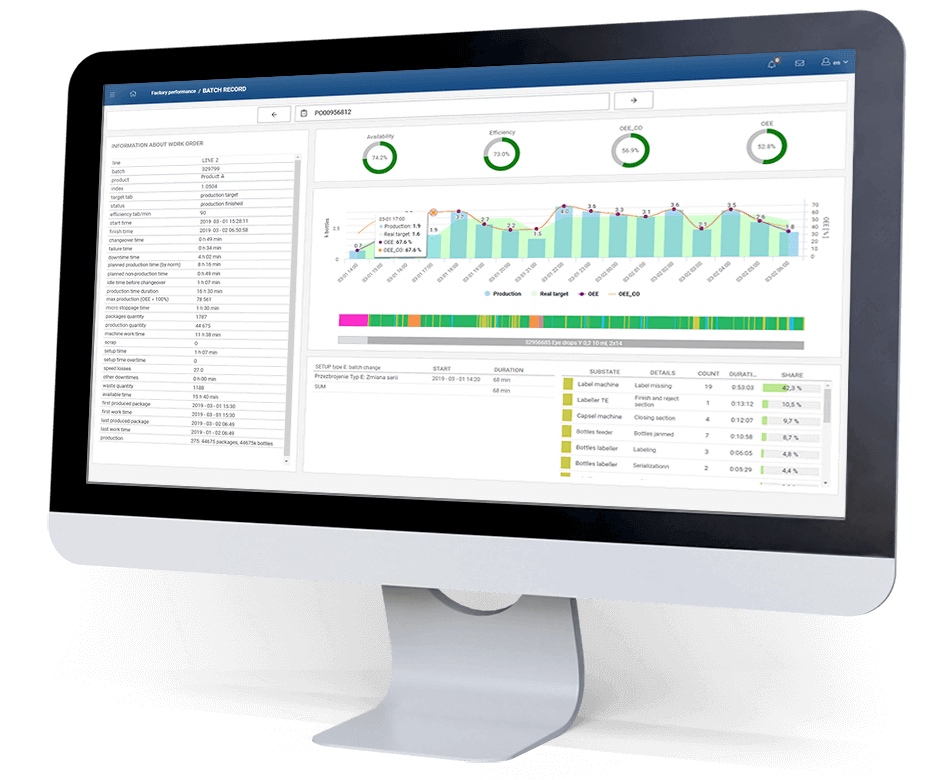
What results have been achieved?
-
- One year after implementation, OEE increased from 44% to 52%
-
- Reduced 27% of micro-dropouts
-
- MTTR value reduced by 33%
-
- A production volume equivalent to one additional packaging line was achieved.
Implementation of an OEE monitoring system – summary of benefits
In the case discussed, it took only three months to implement a ready-made OEE monitoring system without validation. One of the main business objectives was to increase the availability of production lines and this goal was achieved. Reducing micro-downtimes by ¼ and reducing MTTR by ⅓ resulted in an OEE increase of 8% within the first year of implementation.
Related articles

Electronic Batch Records (EBR) Software
Electronic Batch Records (EBR) Software: A Digital Solution for Streamlined Batch Management Electronic Batch Records (EBR) software replaces traditional paper-based batch records, offering digital guidance
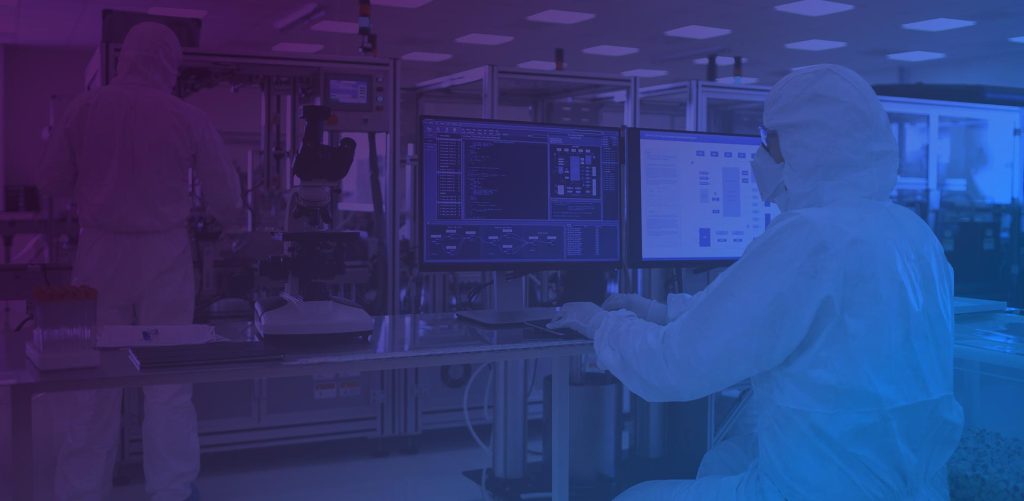
Maintaining Data Integrity in cGMP Compliance
Data integrity is the linchpin of pharmaceutical manufacturing under Current Good Manufacturing Practices (cGMP). It ensures that data generated throughout the manufacturing process is accurate,
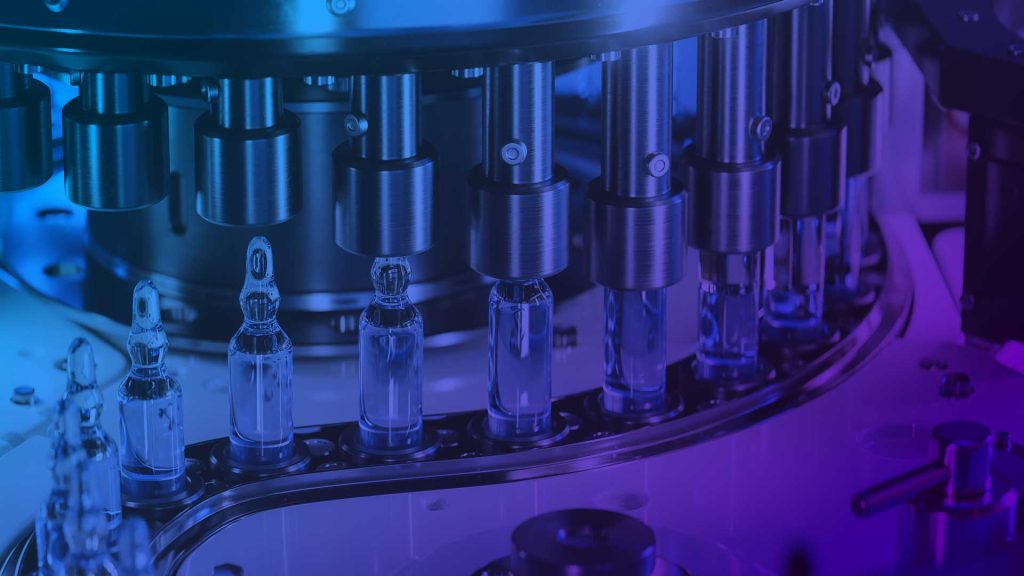
Laboratory Information Management System (LIMS System)
Laboratory information Management System (LIMS) LIMS automates laboratory operations, improving workflow efficiency. Book a Presentation ANT Solutions LIMS ANT Solutions brings you the most comprehensive