Software per accelerare la
produzione
Rendi la tua produzione più efficiente ed ecosostenibile. Eliminiamo gli sprechi, ottimizziamo i processi e riduciamo i costi energetici grazie alla digitalizzazione completa della tua azienda.
ANT SMART FACTORY
Una sola piattaforma. Tante soluzioni per la gestione delle operazioni di produzione
Cosa facciamo
ANT Solutions è un fornitore unico per le vostre esigenze di miglioramento della produzione.

Sviluppo dei
software
Ottieni un sistema modulare pronto per la personalizzazione

Implementazione
Forniamo l'infrastruttura e il collegamento completo

Supporto
continuo
Ottieni un'assistenza 24 ore su 24 e 7 giorni su 7
Cloud Manufacturing
Scopri il potenziale del Cloud Manufacturing: Aumenta l'efficienza, riduci i costi e migliora la qualità dei prodotti. Scegli tra architettura Cloud-Native e On-Premise
- ScalabilitÃ
- AccessibilitÃ
- Agilità e flessibilitÃ
- Migliore utilizzo delle risorse IT
- Servizi cloud aggiuntivi
- Migliorare la sicurezza
- Alta disponibilitÃ
Miglioramento continuo
Potenzia la tua soluzione con più estensioni
Vantaggi per la tua produzione
65%
TEMPI DI REAZIONE PIÙ RAPIDI
- • Dati di produzione in tempo reale
- • Notifiche online per la manutenzione e la qualitÃ
- • Monitoraggio online dell'avanzamento della produzione e della qualitÃ
90%
RIDUZIONE DELLA GENERAZIONE DI REPORT
- • Raccolta automatica dei dati dalle macchine
- • Interfaccia bidirezionale con l'ERP
- • Guida digitale per gli operatori
15%
AUMENTO DELL'OEE
- • Maggiore tempo di funzionamento delle macchine
- • Riduzione dei microstop
- • Meno difetti
Trasforma la produzione in 6 settimane!
Implementeremo il sistema standard in 6 settimane, grazie alla soluzione pronta per l'uso e al metodo di implementazione collaudato

Guida alla digitalizzazione 2024
- Scoprite quali sono i passi fondamentali per la digitalizzazione della fabbrica
- Identifica i problemi principali che si verificano durante la produzione
- Come il software per le fabbriche si adatta ai paradigmi dell'industria 4.0
- Perché la digitalizzazione degli impianti di produzione fallisce?
- Da cosa dipende il prezzo del MES?
- Quali risorse umane devo riassegnare al progetto?
Articoli correlati
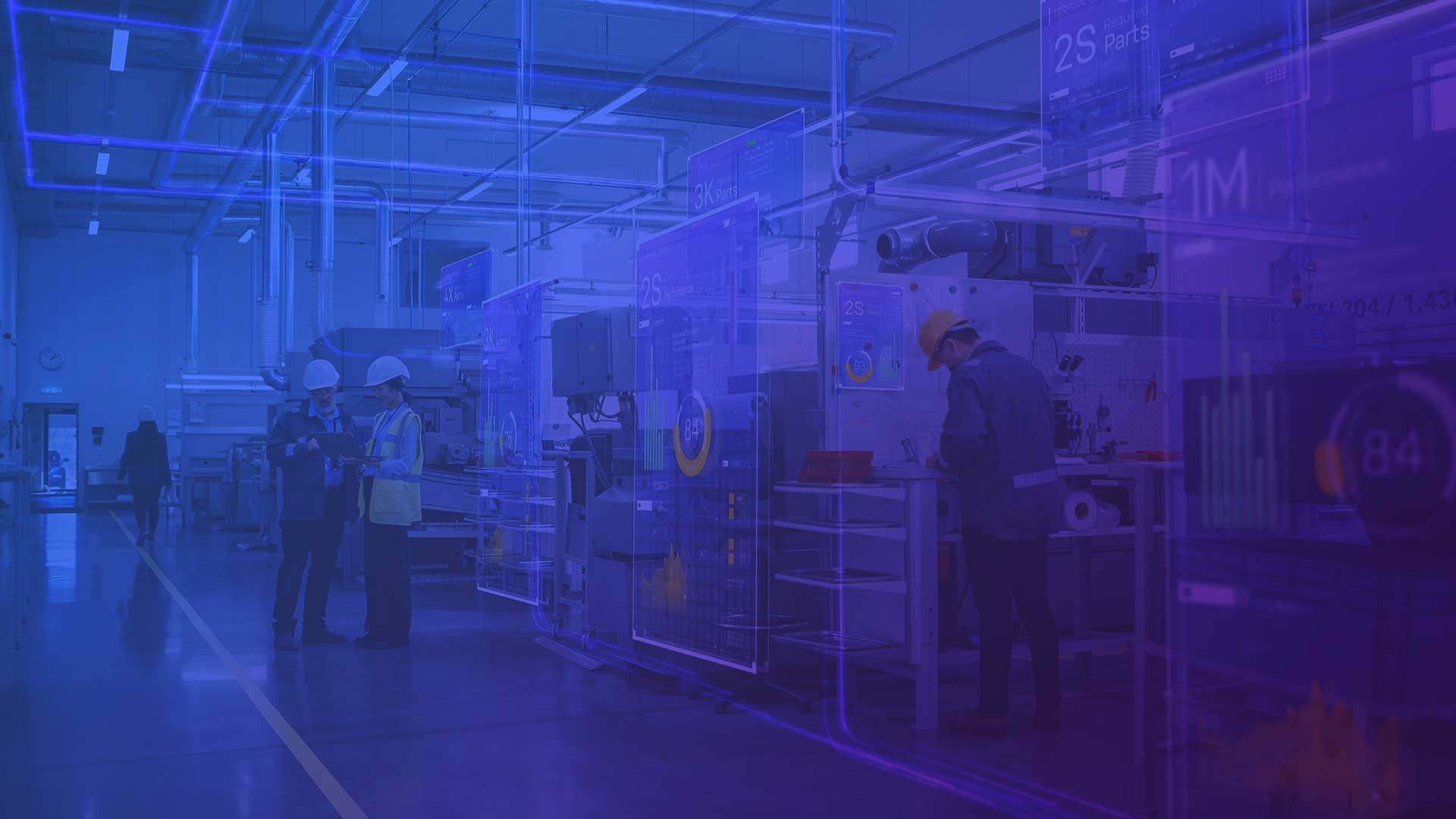
Come funziona il software di acquisizione dei dati delle macchine di produzione?
Il software di acquisizione dei dati macchina è uno strumento che consente di raccogliere, archiviare, elaborare e visualizzare i dati provenienti da macchine e apparecchiature. Questi dati possono essere
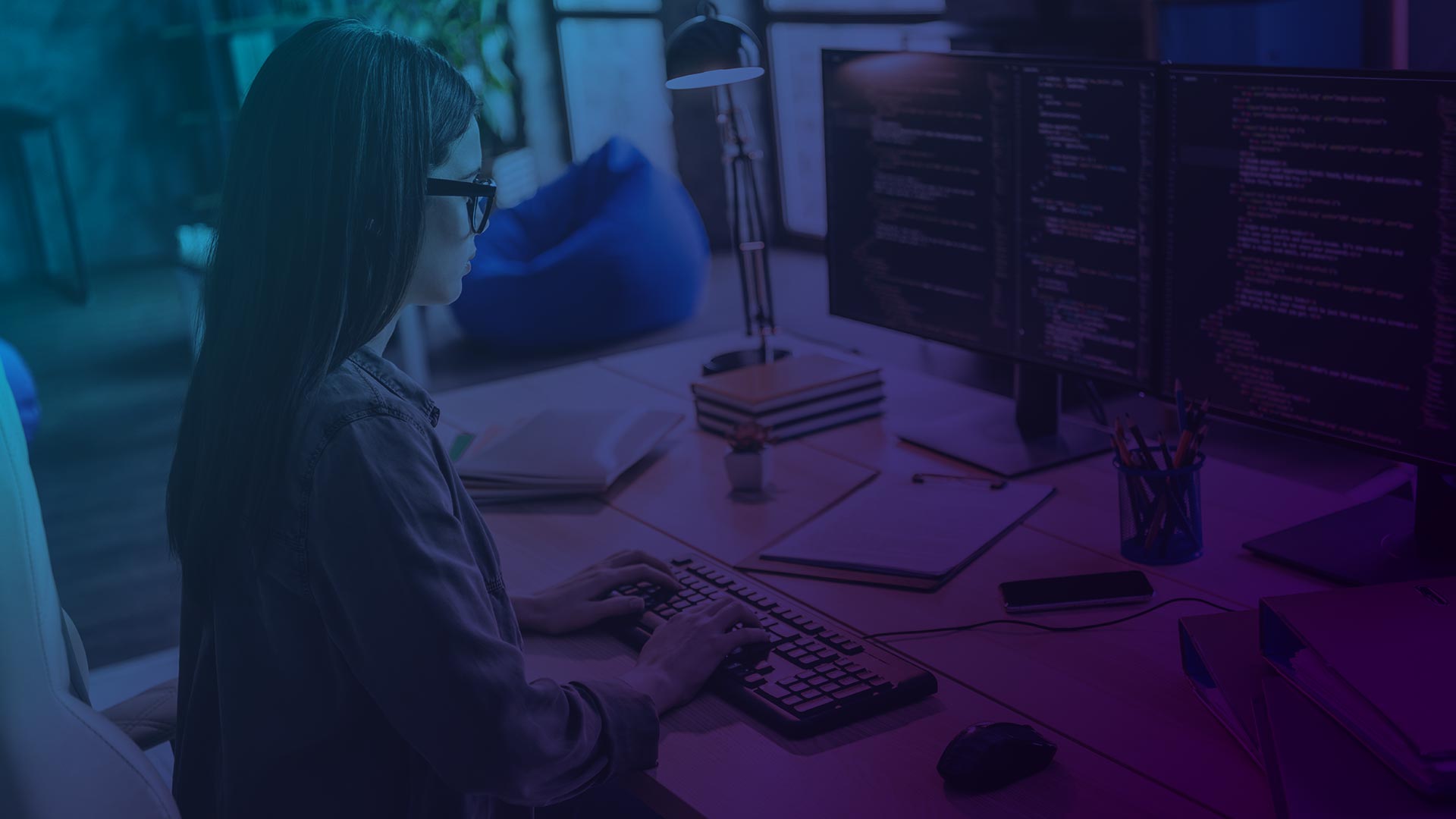
Implementazione del sistema MES, cosa può andare storto?
Il Manufacturing Execution System (MES) è uno strumento software essenziale che aiuta i produttori a raggiungere i loro obiettivi di produzione. Fornisce una panoramica in tempo reale della produzione
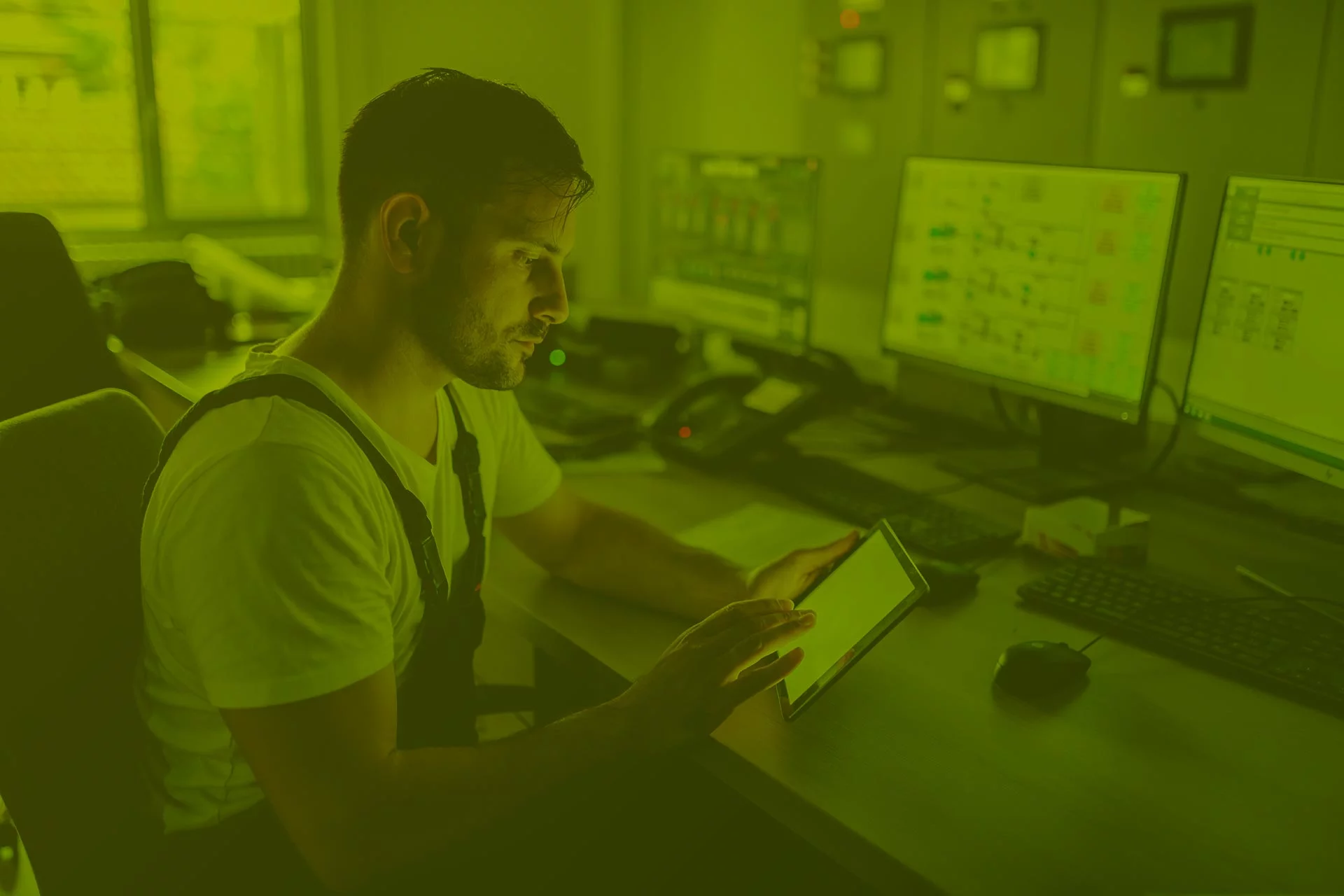
Migliorare la sostenibilità della produzione con i sistemi di gestione dell'energia
1. L'importanza della sostenibilità della produzione Nel mondo di oggi, in cui le preoccupazioni ambientali e le sfide economiche si intrecciano, l'importanza dei modelli e delle pratiche di produzione sostenibili non può essere ignorata.
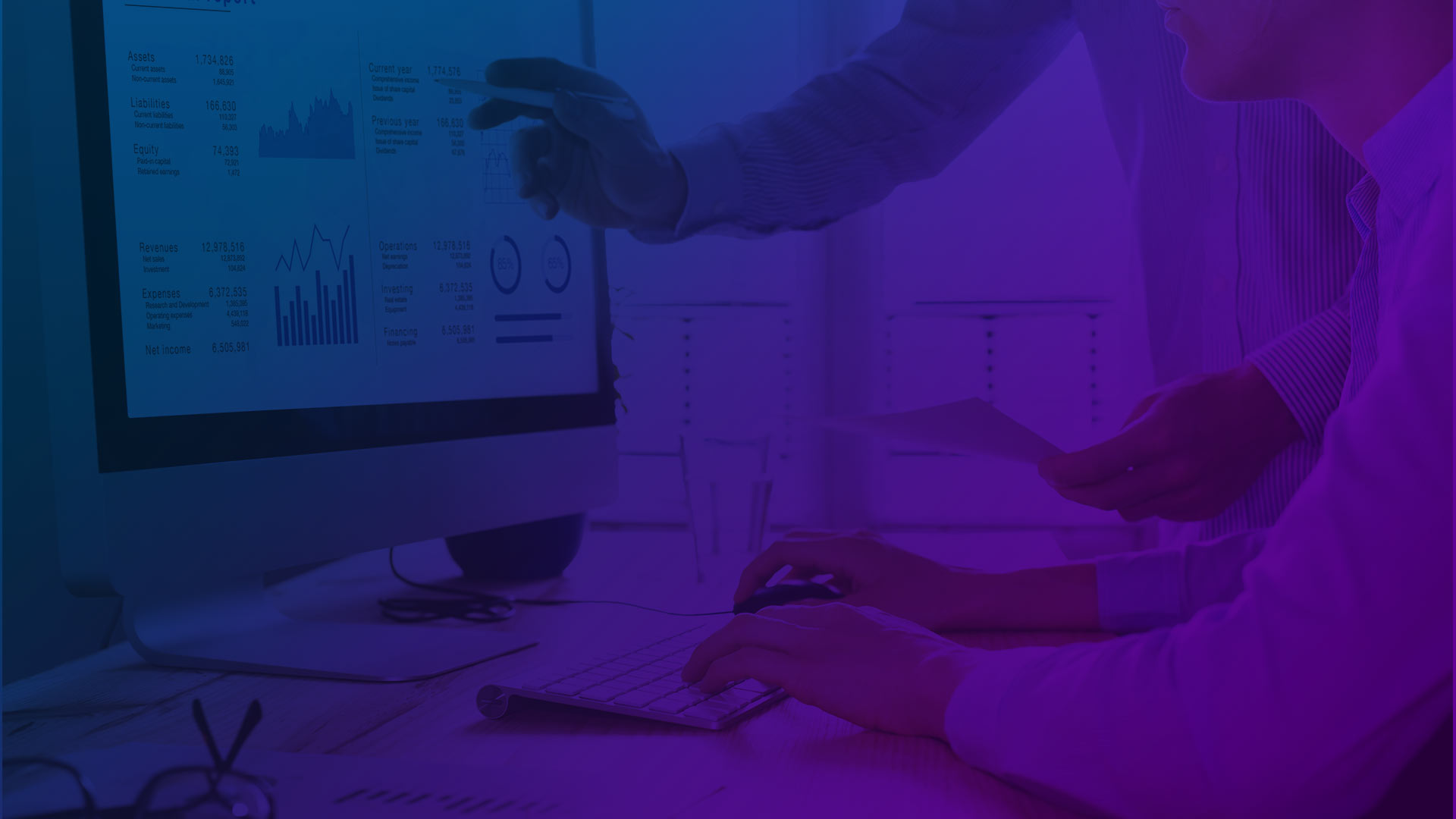
Audit MES: come eseguire la fase di pre-implementazione?
L'implementazione di un sistema MES è un processo complesso e costoso che richiede un'attenta pianificazione e preparazione. Un passo fondamentale è quello di condurre una

In che modo un sistema MES può aiutare ad affrontare le sfide del settore FMCG nel 2023?
L'industria dei beni di largo consumo affronta ogni anno nuove sfide. La produzione in linea con i requisiti governativi e la necessità di soddisfare le aspettative sempre più elevate dei consumatori finali.

Quali sono le cause dei microstoppi durante il processo di produzione?
Imparate a conoscere le cause comuni dei microstoppi durante il processo di produzione e come affrontarle per migliorare l'efficienza e la produttività .